Introduction to LIN
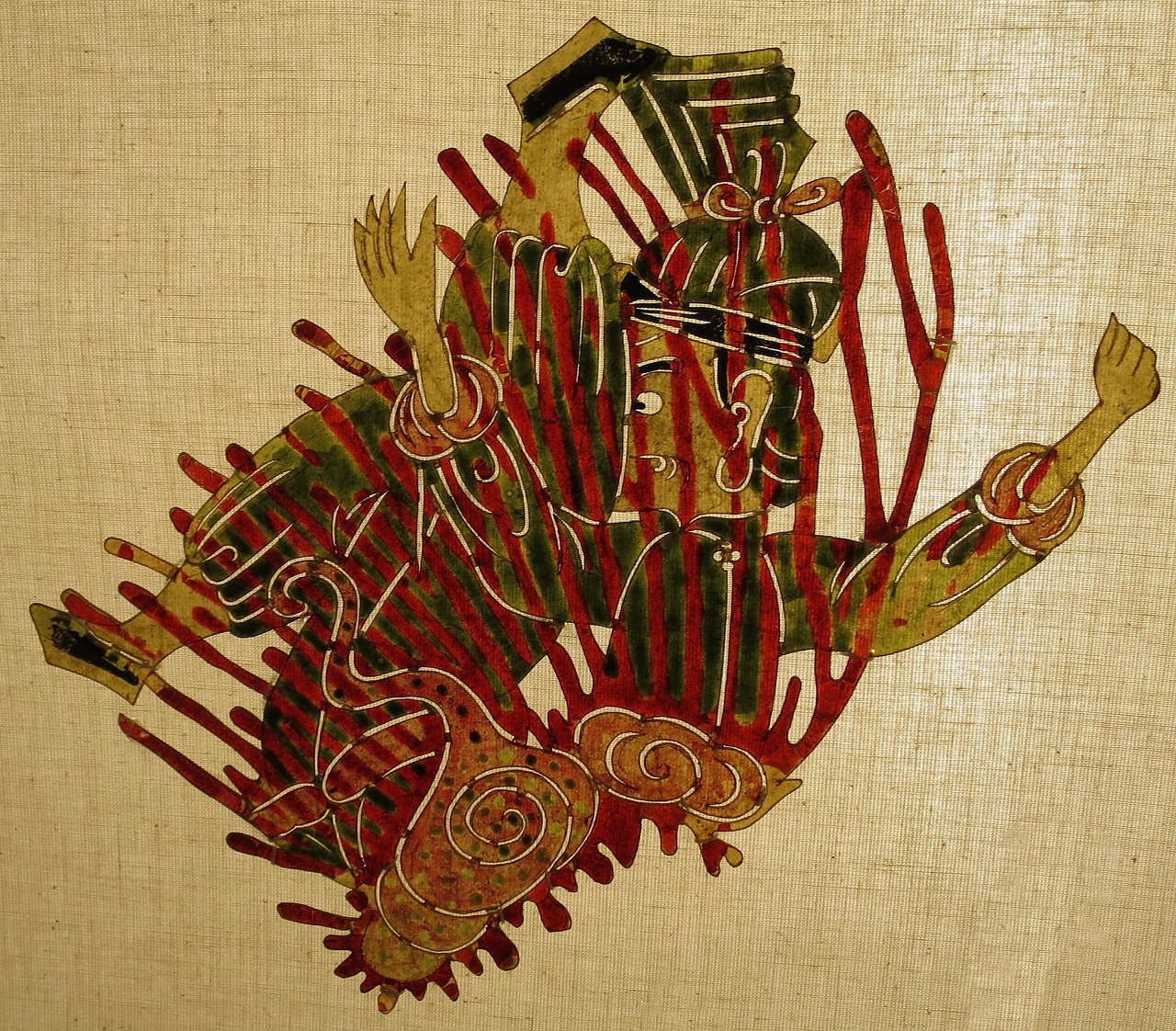
Introduction to LIN: A Comprehensive Guide to Understanding and Implementing LIN in Your Projects
-
What is LIN?
LIN (Local Interconnect Network) is a communication protocol commonly used in the automotive industry. It is designed for low-cost, low-speed data communication between various electronic components in a vehicle, such as sensors, actuators, and control units. LIN allows these components to communicate with each other, enabling the efficient management of vehicle functions and subsystems.
-
How Does LIN Work?
LIN operates on a single wire, reducing the wiring complexity and cost in automotive applications. Each electronic component connected to the LIN bus has a unique address and can send and receive data through the shared communication line. The LIN master initiates communication, while the LIN slaves respond to the master’s requests. The data transmitted over LIN is typically simple, such as sensor readings, status information, and control commands.
-
Implementing LIN in Your Projects
To implement LIN in your projects, you will need LIN transceivers, LIN controllers, and appropriate software libraries or drivers. LIN transceivers translate the electrical signals between the LIN bus and the electronic components, while LIN controllers handle the protocol communication. Additionally, you will need to configure the LIN network, assign addresses to the components, and define the data frames and messages exchanged on the bus. Finally, you can integrate LIN communication into your application code to send and receive data as needed.
-
Benefits of LIN
LIN offers several benefits in automotive applications. It enables cost-effective communication between electronic components, reducing the overall wiring complexity and weight in vehicles. The low-speed communication of LIN is suitable for less time-critical data exchange, such as reading sensors and sending commands for non-essential vehicle functions. Additionally, LIN is widely supported by automotive manufacturers, making it a reliable and widely adopted protocol for implementing various vehicle features and functionalities.
A Reliable Resource on LIN: Examples in Automotive Industry Applications
If you want to dive deeper into the implementation of LIN in the automotive industry, we recommend visiting [insert relevant reliable site address] where you can find comprehensive information, examples, and case studies. This resource offers a hands-on approach to learning about LIN and its applications in various automotive systems and components.
Frequently Asked Questions about LIN:
Q1: Who developed the LIN protocol?
A1: The LIN protocol was developed by a consortium of automotive manufacturers and suppliers known as the LIN Consortium, which includes companies like BMW, Volkswagen, and Bosch.
Q2: Can LIN be used in non-automotive applications?
A2: While LIN was initially designed for automotive applications, its simplicity and cost-effectiveness make it suitable for other industries as well. It can be applied in home automation, industrial automation, and other low-speed communication scenarios.
Q3: What is the maximum data transfer rate of LIN?
A3: LIN supports a maximum data transfer rate of 20 Kbps. Although it is relatively slow compared to other communication protocols like CAN (Controller Area Network), it is sufficient for many non-critical tasks and reduces system complexity and cost.
Q4: Can LIN and CAN be used together in a vehicle?
A4: Yes, LIN and CAN can coexist in a vehicle’s network. They serve different purposes, with LIN being used for low-speed communication between less critical components, while CAN is used for high-speed communication between vital systems and modules.